Unlocking Precision: The Power Of CNC Machining Explained
In the intricate world of modern manufacturing, where precision, efficiency, and repeatability are paramount, one technology stands out as a true game-changer: Computer Numerical Control, or CNC. This revolutionary method has transformed how products are designed and produced, enabling the creation of parts with unmatched accuracy and consistency across countless industries. From aerospace components to medical devices and consumer goods, the impact of CNC machines is ubiquitous, shaping the very fabric of our engineered world.
Understanding CNC goes beyond just knowing the acronym; it delves into the digital revolution of manufacturing. It represents a sophisticated fusion of computer technology and traditional machine tooling, offering unparalleled control and automation. This article will explore the depths of CNC technology, its historical roots, how it operates, its diverse applications, and what the future holds for this indispensable manufacturing powerhouse.
Table of Contents
- What is CNC? A Digital Evolution
- From NC to CNC: A Brief History
- How CNC Machines Work: The Digital Blueprint to Physical Reality
- The Unmatched Advantages of CNC Machining
- A Spectrum of Tools: Types of CNC Machines
- Materials Mastered by CNC
- The Art of CNC Programming and How to Learn It
- The Future of CNC: AI, Robotics, and Optimization
- Conclusion: The Enduring Legacy of CNC
What is CNC? A Digital Evolution
At its core, **CNC** stands for Computer Numerical Control. It is a sophisticated, automated method of controlling machine tools that leverages computer software to program and direct the machinery. Imagine a robot with extreme precision, guided by a digital brain – that's essentially a CNC machine. It represents a significant leap from older, manual machining methods, offering unprecedented levels of accuracy, repeatability, and complexity in manufacturing processes.
- Payne Stewart
- Oregon Historical Society
- Low Porosity Hair
- Where Can I Watch The Truman Show
- Shuckums Oyster Pub Seafood Grill
Unlike traditional machining where an operator manually guides tools, CNC machines interpret a set of digital instructions to perform specific operations. These instructions dictate every movement: how fast the tool moves, its path, its depth of cut, and even tool changes. This digital control ensures that each part produced is virtually identical to the last, a critical factor in mass production and high-precision applications. In essence, CNC machines are a type of industrial robot, meticulously executing pre-programmed commands to transform raw material into finished products.
From NC to CNC: A Brief History
To truly appreciate the advancements of CNC, it's helpful to understand its lineage. The CNC acronym is an outgrowth of an older term: NC, which stands for Numerical Control. Numerical Control refers to the idea of controlling machine tools via coded instructions. The earliest NC machines, developed in the 1940s and 1950s, used punched tapes or cards to feed instructions to the machine. With the older NC term, a computer need not be involved in the direct control loop, though early computers were used to generate the tapes.
The true revolution came in the 1950s when the Massachusetts Institute of Technology (MIT) pioneered the integration of computers directly into the control system. This innovation gave birth to Computer Numerical Control. The early programming languages were quite "primitive" by today’s standards, often involving complex G-code and M-code sequences directly. However, this foundational work laid the groundwork for the powerful, user-friendly software interfaces we see today, transforming what was once a highly specialized, manual craft into a digitally driven, automated process. The shift from NC to CNC marked the transition from fixed, sequential operations to dynamic, software-driven control, opening up a world of possibilities for manufacturing.
How CNC Machines Work: The Digital Blueprint to Physical Reality
The operational principle behind **CNC machines** is a fascinating blend of software engineering and mechanical execution. It begins with a digital design and culminates in a tangible product, all orchestrated by precise computer commands. Both CNC and NC machines work by commanding several tools to make changes to the stock material, but the method of command is where CNC truly shines.
The Role of CAD and CAM Software
The entire process hinges on digital instructions. The CNC machine depends on these digital instructions, which are usually made on Computer-Aided Design (CAD) and Computer-Aided Manufacturing (CAM) software. Programs like SolidWorks or Mastercam are industry standards for this.
- CAD (Computer-Aided Design): This is where the part is designed in a 2D or 3D digital environment. Engineers and designers create a precise virtual model of the desired component. This digital model can represent anything from simple cylindrical symmetry (2D) to complex 3D patterns.
- CAM (Computer-Aided Manufacturing): Once the design is finalized in CAD, it's imported into CAM software. Here, the manufacturing process is planned. The CAM software takes the digital model and translates it into a series of machine-readable instructions, known as G-code and M-code. This code dictates the tool paths, speeds, feeds, and other parameters necessary to machine the part. This code can then be read by the CNC machine tool to construct the physical parts.
Essentially, CNC programming is creating instructions for a CNC machine using software to control how it moves and interacts with the material workpiece. The machine's controller then processes these input instructions and directs the machine tools to perform the desired operations with remarkable accuracy.
The Digital Tool Library and Machine Operations
A key advantage of **CNC machines** is their ability to automatically select and use a variety of tools. With CNC machines, these tools are saved in a digital tool library. This library contains information about each cutting tool, including its size, type, and capabilities. When the CNC program calls for a specific operation, the machine can automatically retrieve the correct tool from its magazine and mount it.
These tools include various types, such as drills, lathes, and mills, which perform the actual machining operations. The machine's axes (typically X, Y, and Z for three-axis machines, with more complex machines having 4, 5, or even more axes) move the cutting tool relative to the workpiece, or vice versa, according to the programmed path. This highly automated process minimizes human error and significantly increases production speed and consistency.
The Unmatched Advantages of CNC Machining
**CNC machines** are an essential technology in modern manufacturing, and for good reason. Their capabilities offer significant advantages over traditional machining methods, leading to higher quality products, increased efficiency, and greater cost-effectiveness.
- Precision and Accuracy: CNC machines are capable of performing complex operations and making precise cuts with high levels of accuracy. This unmatched precision and consistency are critical for industries where tight tolerances are non-negotiable, such as aerospace, medical, and automotive.
- Repeatability: Once a program is created, it can be run countless times, producing identical parts every single time. This is invaluable for mass production and ensuring product quality across large batches.
- Versatility: As we'll explore further, there are countless different types of CNC machines today, capable of various cutting methods and operations. This versatility allows them to handle a wide range of materials and complex geometries.
- Speed and Efficiency: Automated operation means faster production cycles and less downtime. The machine can run continuously, often with minimal human supervision once set up.
- Reduced Labor Costs: While initial investment can be higher, the automation provided by CNC reduces the need for constant manual intervention, lowering labor costs per part in the long run.
- Safety: Operators are less exposed to moving parts and cutting tools, significantly improving workplace safety compared to manual machining.
- Complex Geometries: CNC machining allows for the rapid but highly accurate construction of projects from materials that are not suited to other types of rapid prototyping manufacturing, such as 3D printing. It can create intricate shapes and features that would be impossible or extremely difficult to achieve manually.
These advantages collectively make CNC machining a cornerstone of modern industrial production, enabling innovation and driving progress across diverse sectors.
A Spectrum of Tools: Types of CNC Machines
The term **CNC machine** encompasses a vast array of machine tools, each designed for specific tasks and materials. CNC machines are machine tools that cut or move material as programmed on the controller. The type of cutting can vary widely, from material removal processes to shaping and forming.
CNC Lathes: The Art of Turning
One of the most common types of CNC machines is the lathe, specifically a CNC turning machine. CNC turning tools are made to work with these machines. CNC lathes rotate workpieces at high RPMs (revolutions per minute) to shape the workpiece. A stationary cutting tool then removes material from the rotating part, creating cylindrical symmetry (2D) and sometimes more complex 3D patterns, especially with live tooling.
Lathes are accurate and can handle tough materials, just like other CNC machines. Due to the high rotational speeds and the use on hard materials like metals, the friction produced can result in high temperatures, which necessitates proper cooling systems and tool material selection. CNC lathes are essential for producing shafts, pins, bolts, and many other round components.
Beyond Turning: Milling, Routing, and Plasma Cutting
Beyond lathes, the diversity of CNC technology is truly impressive:
- CNC Mills: These machines use rotating cutting tools to remove material from a stationary workpiece. They are incredibly versatile, capable of producing flat surfaces, slots, holes, and complex 3D shapes. They come in various configurations, including 3-axis, 4-axis, and 5-axis machines, offering increasing levels of complexity and freedom of movement.
- CNC Routers: Similar to mills but typically used for softer materials like wood, plastics, composites, and some non-ferrous metals. They are common in woodworking, sign making, and furniture production.
- CNC Plasma Cutters: These machines use a high-temperature plasma torch to cut through electrically conductive materials, primarily metals. Plasma systems often include closed-loop digital torch height control for precise cuts.
- CNC Laser Cutters: Employ a focused laser beam to cut, engrave, or mark a wide range of materials, including metals, plastics, wood, and fabric. They offer extremely high precision and a clean finish.
- CNC Waterjet Cutters: Use a high-pressure stream of water, often mixed with abrasive particles, to cut through virtually any material, including very thick metals, stone, and glass, without generating heat.
- CNC Grinders: Used for finishing operations, providing very high surface finishes and tight tolerances.
- Robotic CNC: Some advanced CNC systems can even pick up and move items on an assembly line, showcasing their versatility beyond just cutting.
This broad spectrum of machines means that for almost any manufacturing task involving material manipulation, there's a **CNC** solution available, capable of delivering superior results.
Materials Mastered by CNC
One of the significant strengths of **CNC machining** is its ability to handle a vast range of materials. This versatility makes it an indispensable technology across virtually every industry.
- Metals: This is the most popular and common material used with CNC machines, especially since nearly any metal is fair game. This includes:
- Aluminum: Lightweight, excellent machinability, used in aerospace, automotive, and consumer electronics.
- Steel (Stainless, Carbon, Alloy): Strong, durable, used in construction, automotive, and industrial machinery.
- Brass and Copper: Good electrical conductivity, often used for electrical components and decorative items.
- Titanium: High strength-to-weight ratio, biocompatible, used in aerospace, medical implants, and high-performance applications.
- Exotic Alloys: Nickel-based alloys, superalloys used in extreme environments like jet engines.
- Plastics: CNC machines are excellent for prototyping and producing plastic parts with high precision. Common plastics include:
- ABS (Acrylonitrile Butadiene Styrene): Common for consumer products, good impact resistance.
- Nylon: Strong, wear-resistant, used for gears, bearings.
- Delrin (Acetal): High stiffness, low friction, used for precision parts.
- Polycarbonate: Transparent, high impact strength, used for optical components.
- PEEK (Polyether Ether Ketone): High-performance plastic, excellent chemical and temperature resistance, used in medical and aerospace.
- Composites: Materials like carbon fiber, fiberglass, and other reinforced plastics are increasingly machined with CNC for lightweight, high-strength applications in aerospace and sports equipment.
- Wood and Wood Products: CNC routers are widely used for furniture, cabinetry, signage, and artistic carvings.
- Foams: Used for prototyping, model making, and insulation.
- Wax: Often used for creating molds for investment casting.
The ability of **CNC machines** to work with such a diverse material palette underscores their adaptability and crucial role in meeting the varied demands of modern manufacturing.
The Art of CNC Programming and How to Learn It
At the heart of every successful **CNC machining** operation lies effective programming. CNC programming is the process of creating instructions for a CNC machine using software to control how it moves and interacts with the material workpiece. While modern CAM software automates much of this, understanding the underlying principles and even manual G-code is invaluable for machinists.
The language used to control CNC machines, often G-code (geometric code) and M-code (miscellaneous functions), dictates every action: rapid movements, linear and circular interpolation, tool changes, coolant on/off, spindle speed, and more. While the language itself might seem "primitive" compared to high-level programming languages, its precision is absolute.
So, how to learn CNC programming? The best way to learn CNC programming is often through a combination of theoretical knowledge and hands-on experience.
- Formal Education: Many vocational schools, community colleges, and technical institutes offer programs in CNC machining and programming. These programs provide a structured curriculum covering CAD/CAM software, G-code, machine operation, and safety.
- Online Courses and Tutorials: Numerous online platforms offer courses ranging from beginner to advanced levels. These can be a flexible way to learn the theoretical aspects and software skills.
- Apprenticeships and On-the-Job Training: Arguably the most effective method for practical skills. The best way to learn CNC programming is to find a CNC shop that is hiring and start as a machine tool operator. This allows you to learn from experienced machinists, troubleshoot real-world problems, and gain invaluable hands-on experience with various machines and materials.
- Self-Study: Reading textbooks, programming manuals, and practicing with simulation software can build a strong foundation.
A good CNC programmer not only understands the code but also has a strong grasp of machining principles, material science, and tool selection. It's a blend of technical expertise and practical artistry.
The Future of CNC: AI, Robotics, and Optimization
The world of **CNC machining** is not static; it's constantly evolving, driven by advancements in artificial intelligence, robotics, and the relentless pursuit of optimization. These innovations are pushing the boundaries of what CNC machines can achieve, making them even more intelligent, autonomous, and efficient.
- Robotic Assistance and Automation: The latest upgrades for some CNC machine models include the introduction of robotic assistance. This allows the CNC machinist to load a specific number of raw materials or blanks into the input magazine of the machine, and the CNC machine will work its way through the supplied inventory using automated robotic subroutines. This level of automation significantly reduces manual labor, increases throughput, and allows for lights-out manufacturing (production without human presence).
- Artificial Intelligence (AI) and Machine Learning: AI is poised to revolutionize CNC operations. Artificial intelligence can forecast periods of servicing and equipment of CNC machine tools structures by linking to production data such as machine performance and tool life. This predictive maintenance minimizes unexpected downtime, a major cost factor in manufacturing. AI can also optimize cutting parameters in real-time, adapting to material variations and tool wear to achieve better surface finishes, faster cycle times, and extended tool life.
- Optimization for Profitability: The CNC machining operations must be optimized in order to save money and time and increase overall profit per production period [15]. This includes not just machine performance but also workflow, inventory management, and energy consumption. AI and advanced analytics play a crucial role in identifying bottlenecks and inefficiencies, allowing manufacturers to maximize their return on investment.
- Additive Manufacturing Integration: While often seen as separate, there's a growing convergence between CNC (subtractive manufacturing) and additive manufacturing (3D printing). Hybrid machines that can both print and machine a part are emerging, offering new possibilities for complex geometries and material combinations.
- Industry 4.0 and IoT: CNC machines are increasingly connected to the Industrial Internet of Things (IIoT), allowing for real-time data collection, remote monitoring, and integration into larger smart factory ecosystems. This connectivity enables better decision-making, improved supply chain management, and greater overall operational visibility.
These advancements ensure that **CNC technology** will remain at the forefront of manufacturing innovation, continuing to drive efficiency, precision, and new capabilities for decades to come.
Conclusion: The Enduring Legacy of CNC
From its humble beginnings as Numerical Control to the sophisticated, AI-powered systems of today, **CNC technology** has undeniably reshaped the landscape of modern manufacturing. It stands as a testament to human ingenuity, bridging the gap between digital design and physical reality with unparalleled precision and consistency. CNC machines are not just tools; they are the silent, tireless workhorses that enable the production of everything from the smallest, most intricate medical implants to the largest, most critical aerospace components.
The ability of CNC to handle a vast array of materials, perform complex operations with high accuracy, and adapt through advanced programming and automation makes it indispensable. As we look to the future, with the integration of robotics, artificial intelligence, and the principles of Industry 4.0, the capabilities of CNC will only continue to expand, promising even greater efficiency, innovation, and profitability for industries worldwide.
What are your thoughts on the impact of CNC in your daily life, or perhaps in your industry? Share your experiences and insights in the comments below! If you found this article insightful, consider sharing it with your network or exploring other related articles on our site to deepen your understanding of manufacturing technologies.
- Amanda Brumfield
- Payne Stewart
- Thomas Shelby
- %C3%A9%C2%BA %C3%A8%C3%A5 %C3%A9 %C3%A5%C3%BF
- Detroit Lions Vs 49ers Match Player Stats
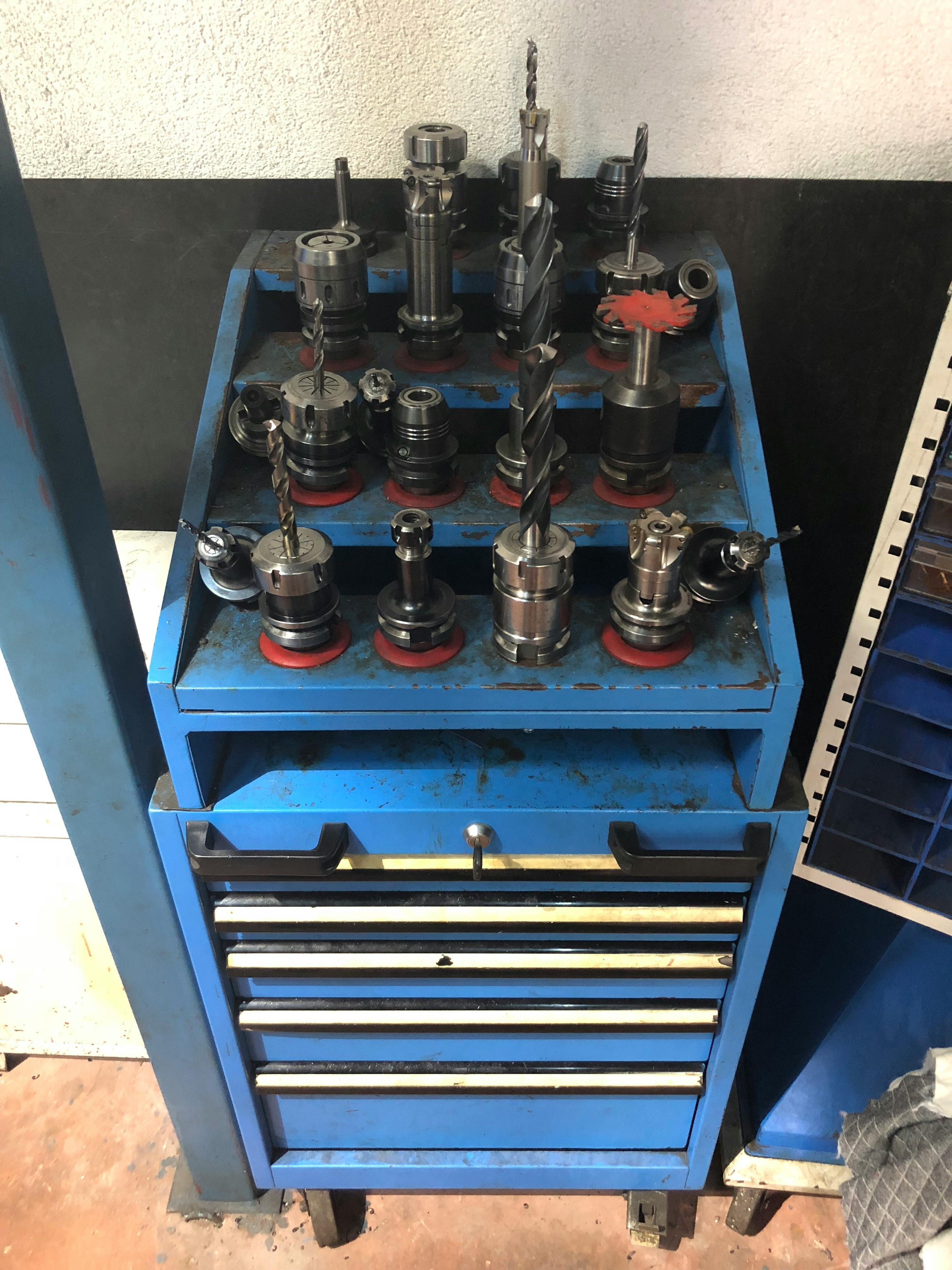
Free stock photo of cnc
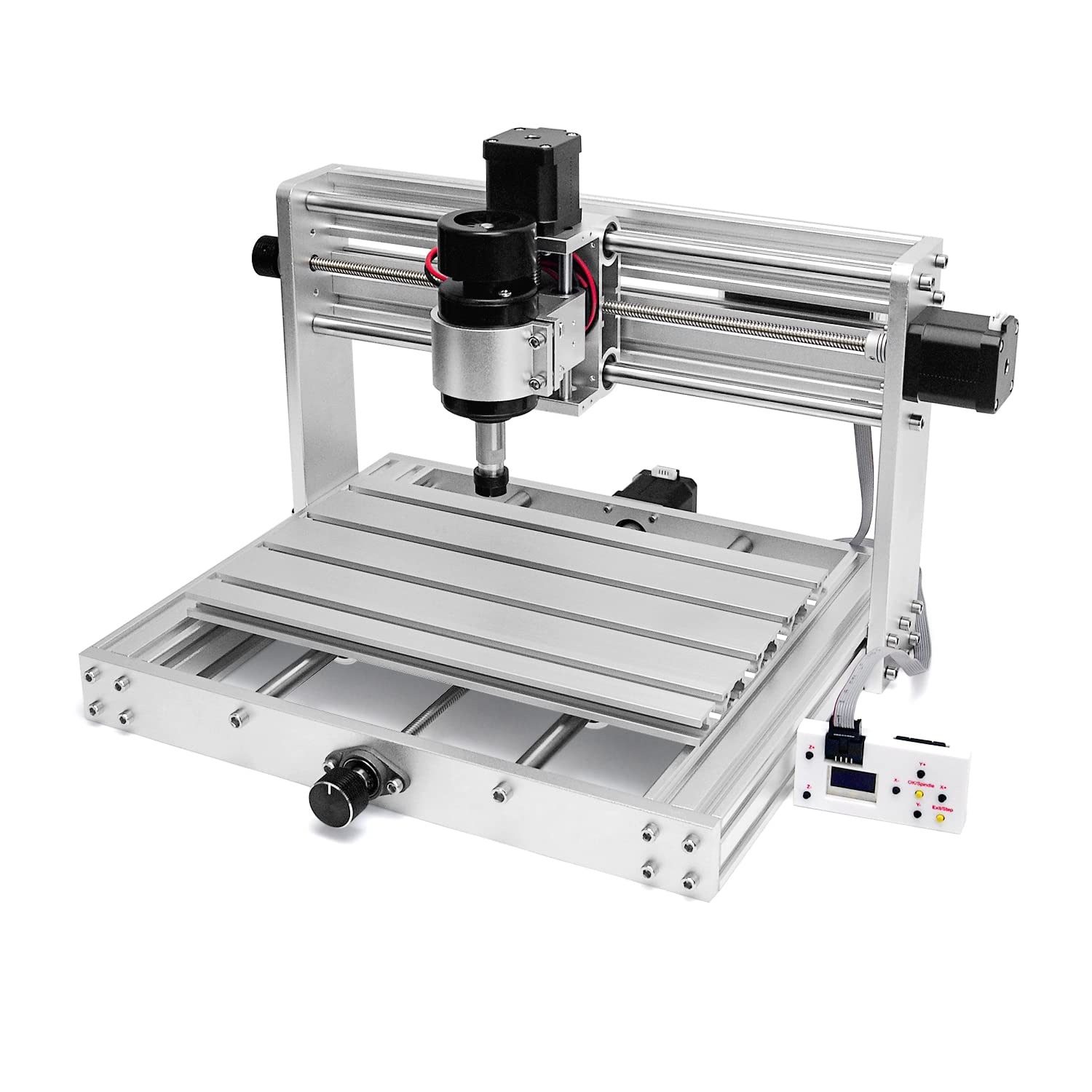
3018 CNC Software

Browse CNC machines by process